在庫管理の見える化とは?導入メリットと具体的な手法をについて解説します。
「今の在庫管理がアナログすぎる...」
「手動の在庫の見える化はしているけどミスが多い」 「もっと在庫管理を効率化して人件費を減らしたい」 という方のために、物流コンサルティング会社の現役COOが効率的な在庫管理の仕方について、徹底解説致します。
「どんな在庫管理システムを使用すればいいの?」 「自分に合った在庫の見える化を行いたい」
という方向けに記載していきます。
在庫の見える化とは?
在庫の見える化とは、在庫状況を誰が見てもすぐに確認できるようにすることです。
在庫の見える化では、「現品」と「情報」の両方で見える化を進める必要があります。
現品の見える化:在庫の場所を見て分かるようにする
情報の見える化:在庫の数量を数えて記録を残す
現品の見える化のために、在庫の置き場を決めて守ること、情報の見える化のために、入出庫のたびに記録をとること、というように継続してルールを守ることが必要になってきます。
また、在庫の見える化をするためには、「場所を把握して管理を行う」「システムやExcel等で商品の在庫状況を記録を行う」といったことを実行する必要があります。
これらをきちんと実行できれば、倉庫内の「在庫切れ・過剰在庫の防止」「業務効率化の促進」「コスト削減」につなげることが可能です。GPSによる位置情報や地図ソフト、ネットワークを活用して、トラックや一般車の運行計画や走行(配送)ルートを効率的に作成・管理するシステムのことです。
配車システムは主に「配車管理システム」「自動配車システム」「車両管理システム」の3種類があります。
「在庫を見える化」するメリット
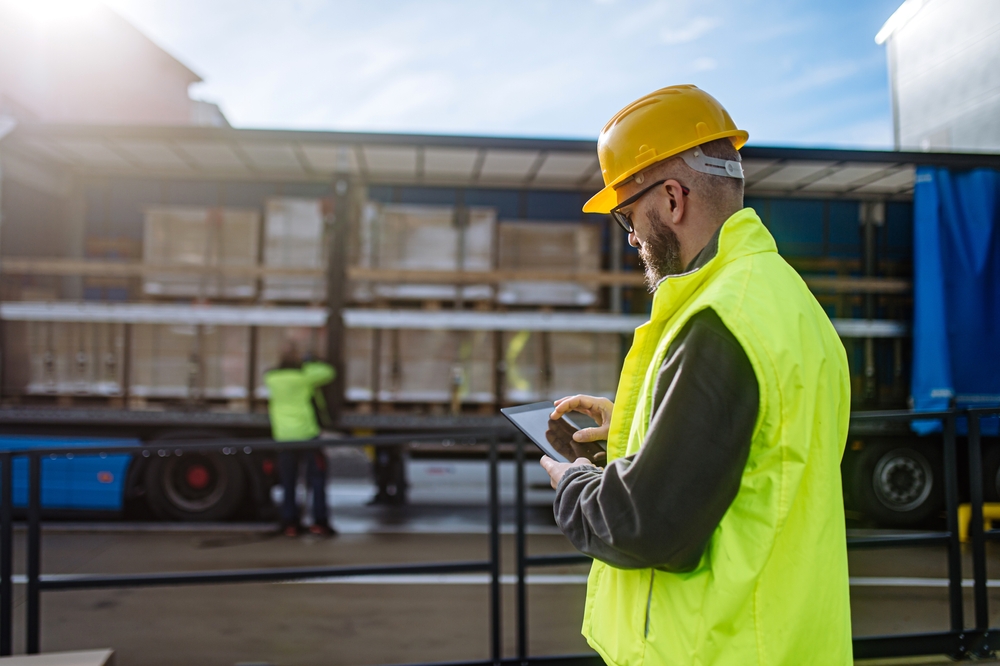
①在庫切れや過剰在庫を防ぐことができる
在庫切れ、過剰在庫は、販売の機会損失・品質の低下による廃棄のため企業の不利益に繋がる恐れがあります。在庫の見える化を徹底すると、適正な数の在庫を発注することが可能になります。
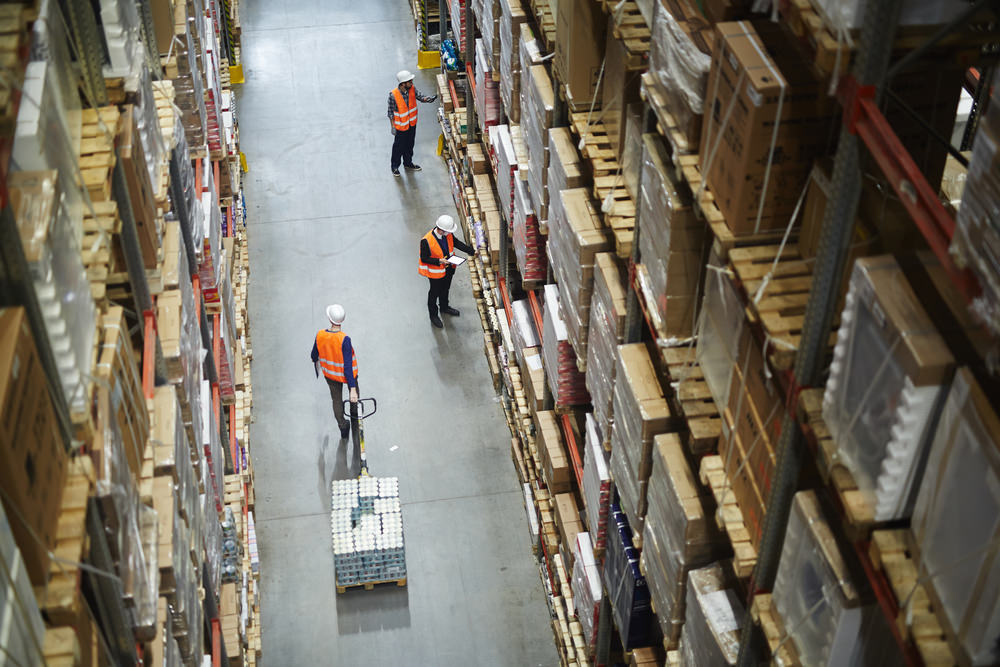
②業務効率化が期待できる
たとえば、在庫の見える化をしていない場合は、発注が必要な商品を倉庫内で見て回り、一つ一つの数量をチェックしなければなりません。
また在庫確認を一部の専門のスタッフに任せてしまっていると発注の度に商品の在庫場所を把握しているスタッフへの確認が必要になり、効率が悪いだけでなく属人化の温床となります。
在庫の見える化ができていれば、誰でもすぐ商品状況を確認でき、発注時間の短縮につながります。更にピッキングの際、出荷商品を探し回る必要がなくなります。在庫の見える化では、倉庫内で在庫保管場所を割り振り、必要な商品がどの場所にあるか一目でわかるようになります。
その対象商品が「どこに」「どれだけ」あるかをすぐに確認できるようになり、効率的なピッキングが可能になるのです。
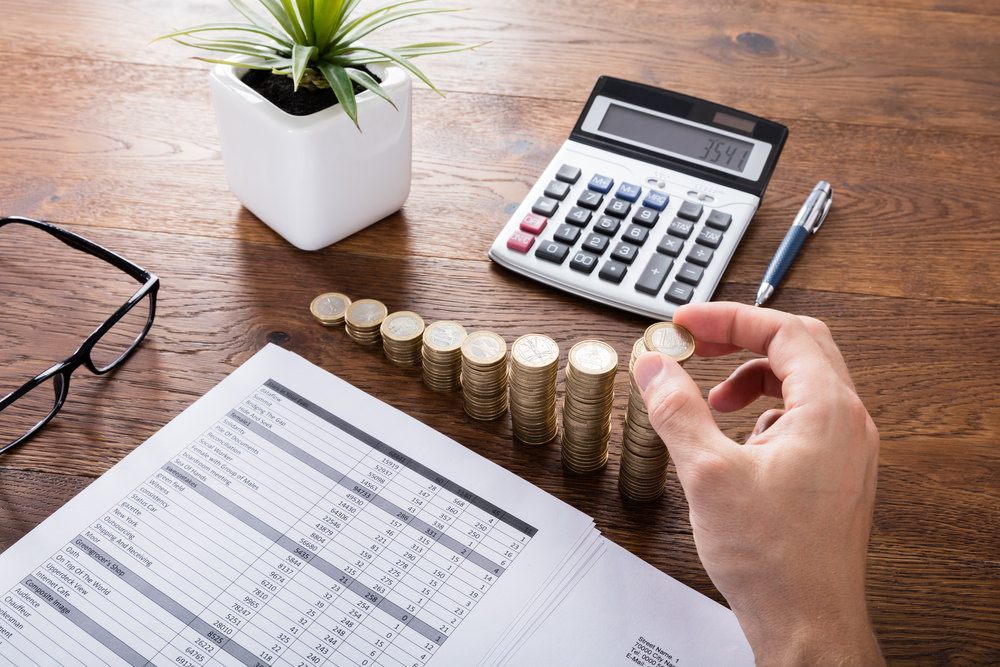
③コスト削減につながる
しかし、在庫管理システムなどを導入する場合、システムの導入費用がかかってしまうので、削減できる費用や創出されるコストメリットとのバランスを見なければなりませんが、物量の多い倉庫ほど、在庫の見える化による無駄の削減効果は大きいです。
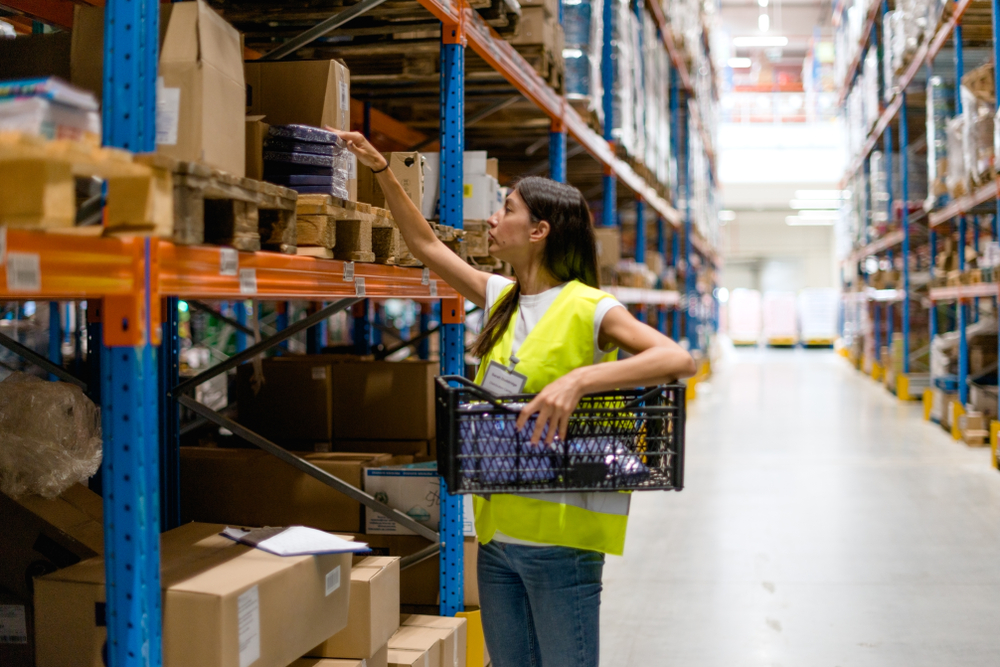
④商品品質が保持される
在庫の見える化を行うことにより、古い商品から先に出荷していくという仕組みが構築できるため、商品品質の保持が可能となります。
効率的に在庫を見える化する方法
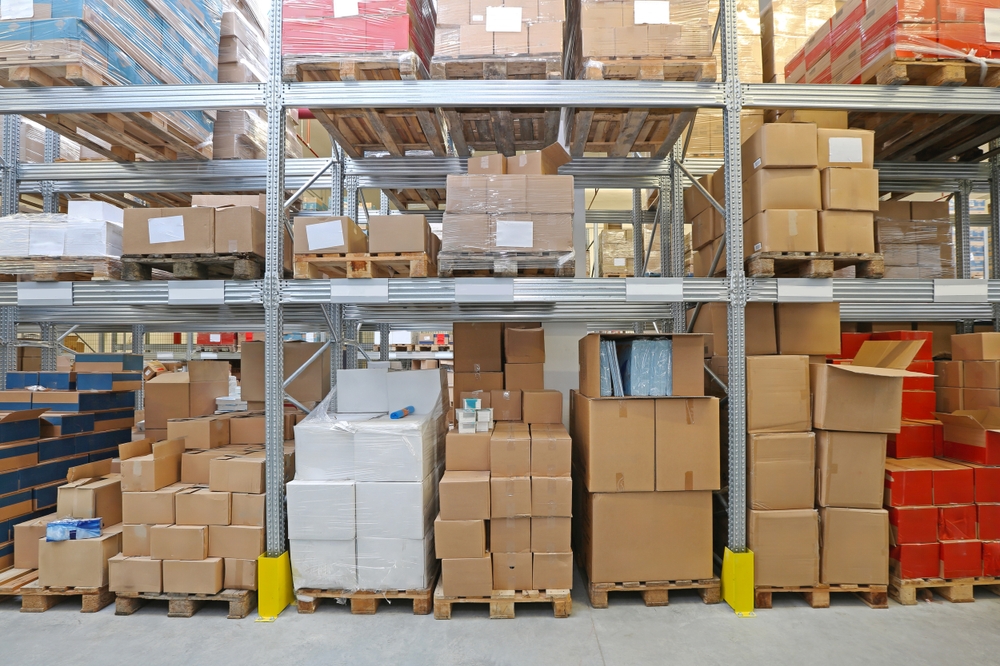
①ロケーション管理を行う
ロケーション管理をすることにより、
・在庫商品の正確な位置
・在庫商品の状態
をすぐにわかるようになり、倉庫作業をより効率的に行うことが可能になります。

②在庫管理システムを導入する
・在庫の一覧を確認することができる機能(商品の種類ごとに在庫数を確認または管理できる機能)
・入出荷を管理することができる機能(入出荷する商品を記録を行う機能)
・検品の際の管理機能(入出庫する商品の数量や品目に間違いがないかをチェックする機能)
・棚卸を行う機能
もちろん導入には費用がかかりますが、作業効率や保管効率をアップさせることができることを考えると、結果的にはコストの削減につながるサービスといえます。
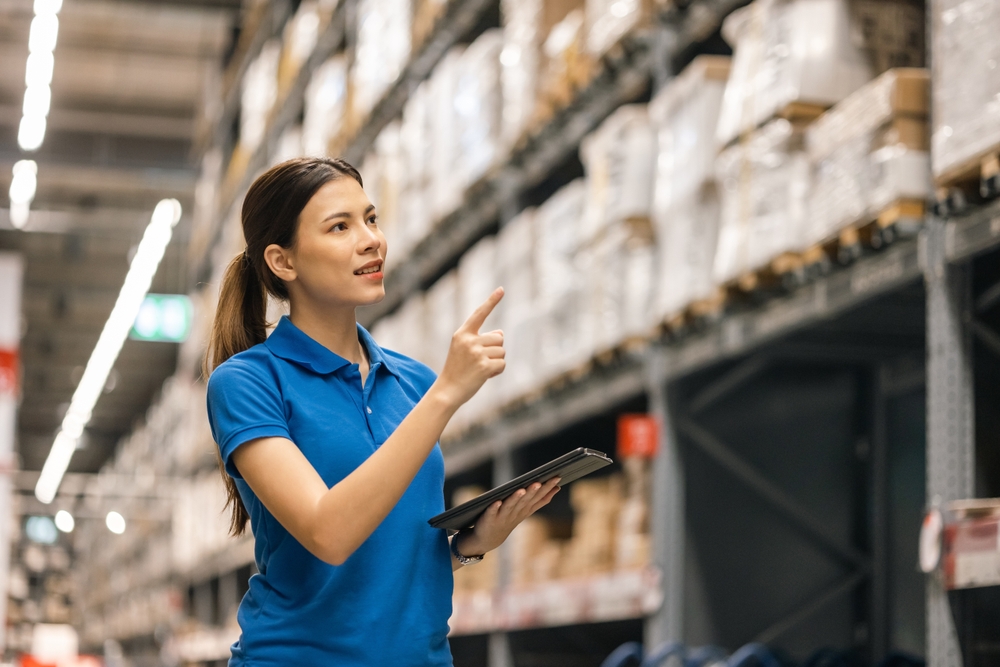
③5Sを徹底させる
整理:不要なものと必要なものを分け、不要なものは処分すること
整頓:散らかり乱れている物を、きちんとかたづけ整った状態にすること
清掃:きれいに掃除すること
清潔:きれいで整った状態をキープすること
躾(しつけ):清潔な状態をキープするよう習慣づけること
5Sを徹底させることで、
・「商品の在庫の所在がわからない」
・「在庫が多いことや、片付けられてないことにより作業スペースが狭くなっている」
・「倉庫内の管理がゆきとどかず、在庫の管理状態も悪くなってしまった」といったことを防ぐことが可能です。
5Sを徹底させることは、倉庫内のスタッフの教育や意識により行うことができるので、常に意識し習慣付けをすることが必要になります。
在庫を見える化する際の注意点
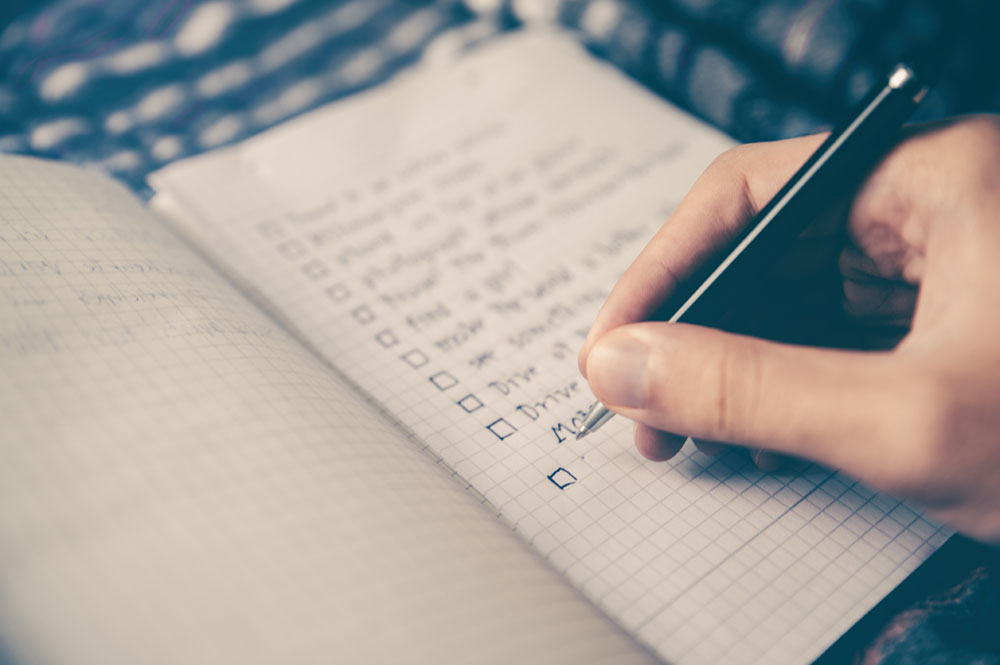
①マニュアルを作る
スモールスタートで不備がないかを確認し、課題が見つかれば解決策を検討します。在庫管理システムを問題点なく運用できると感じた時点で、マニュアルを作成し、本運用を開始します。以降はシステムの操作方法をコンスタントに見直し、利用者の満足度が向上するようにマニュアルを更新するのが望ましいです。
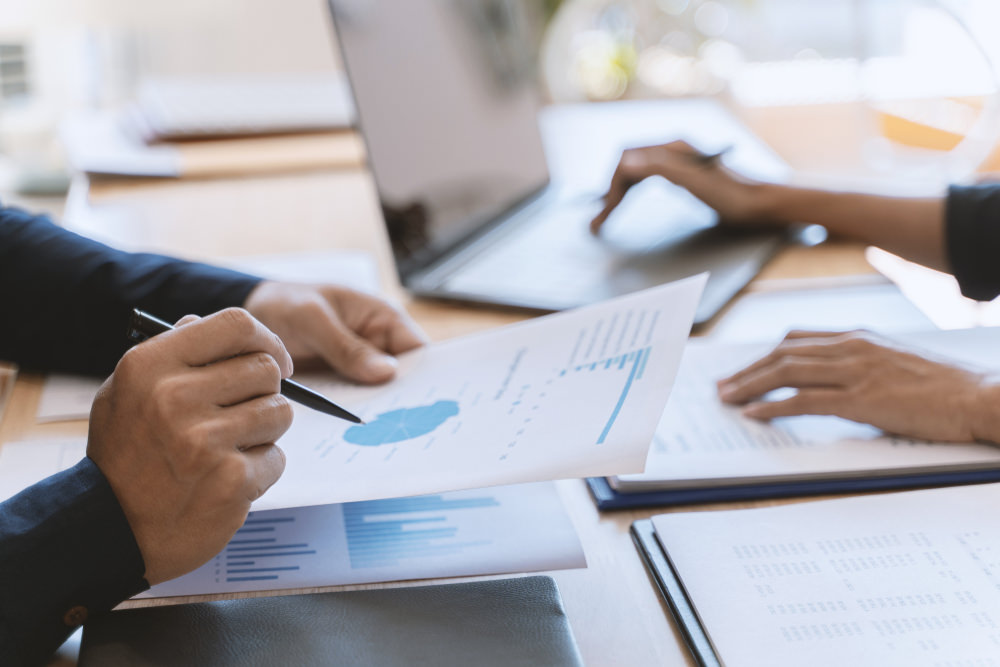
②自社に合うシステムを選ぶ
弊社シーオスでは、現場経験ある物流コンサルタントが貴社の問題発掘から最適なシステム制作、導入サポートまで手厚くサポート致します。詳しくは下記のページをご覧ください。
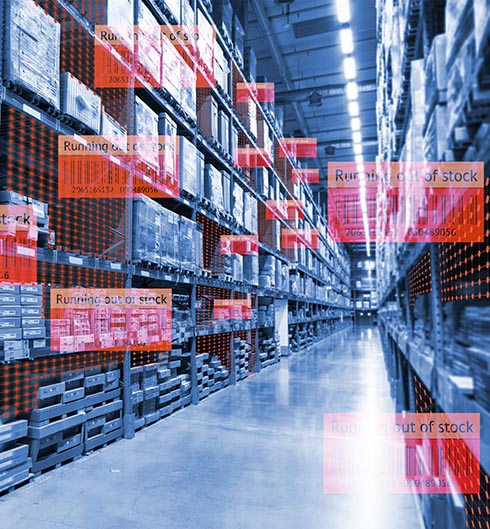
③倉庫全体に入れることのできる在庫の量を事前に把握しておく
在庫数の現状を把握するためには、以下の段階を踏むことが大切です。
・保管可能なキャパシティの把握
・残材在庫量の把握
・整理・整頓
・入出庫傾向の把握
整理・整頓により、適正状態の在庫を正しく把握、管理できるようになり、入出庫傾向を把握することで、今後の在庫変動の推測が可能となります。
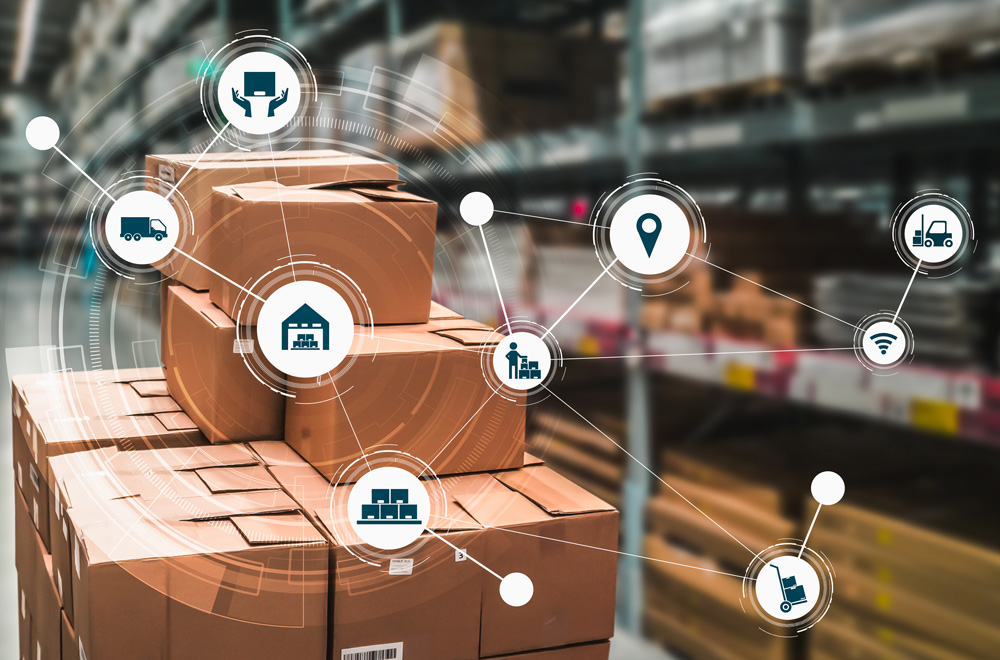
④適正在庫のあり方を決める
続いて、売上等の把握を行いながら、適正な在庫数の基準についてしっかりとコントロールすることにより、欠品による無駄な損失、余ってしまう在庫による保管コストの無駄を防止できるようになります。
在庫管理システムの導入事例

①化粧医薬品ネット通販会社の例
最終的には、業務効率化により人件費等が削減されたため、提供商品の値引きや送料無料キャンペーンなどの実施を可能にし、結果として昨年比150%の売上を達成に貢献しました。
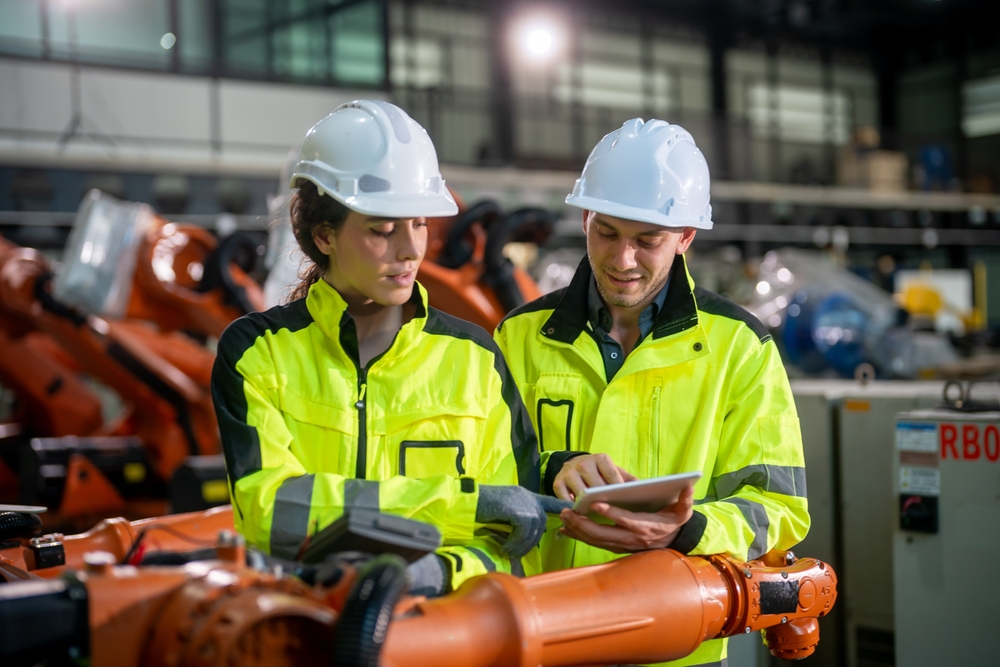
②製造業会社の例
そこで、在庫管理システムを導入することで改善策が講じられました。システム導入により、製造工場と本社の双方で在庫情報をリアルタイムに共有することが可能となり、予定納期、工程進捗状況、商品状態毎の在庫状況などの一括管理が可能となりました。また、情報共有もしやすくなり、生産管理から在庫管理までのスピードを向上させることができました。
まとめ:物流倉庫の問題解決はシーオスが全て解決します
弊社シーオス株式会社は
・全て手作業で行っていたが最近ミスが多いのでDX化を進めたい
・DX化を進めたいけど、具体的に何から始めればいいか全く分からない
・ヒューマンエラーが多すぎるので、マテハン・ロボットに変えて正確に作業を行うような環境を構築したい
などの課題を現場経験のある物流コンサルタントとDXの力を組み合わせ貴社にとって
管理コストを最小限に押さえて貴社にカスタマイズした使いやすいシステムの導入を支援します。作業の機械化を進めたい方は下記のボタンよりお問い合わせくださいませ。
ロジスティクス大賞の受賞で裏付けられる
技術とノウハウ
シーオスは、公益社団法人 日本ロジスティクスシステム協会が主催する「 ロジスティクス大賞」を2度受賞しています。
その他の記事
- 物流業界の課題を解決する「物流DX」とは
- 「WMS」について詳しくご紹介
- 「OMS」について詳しくご紹介
- 「AMR」について詳しくご紹介
- 「3PL」について詳しくご紹介
- 「物流センターの自動化」について詳しくご紹介
- 「物流センターの省人化・無人化」について詳しくご紹介
- 「AGV(無人搬送車)とは?AMR(自動搬送ロボット)との違いや導入のメリット」について詳しくご紹介
- 自動倉庫とは?導入のメリット・デメリットや注意点、事例などについて解説します。
- PSIとは?在庫最適化の実現に向けた注意点や具体的な方法について解説します。
- 倉庫レイアウトとは?効率の良い倉庫レイアウトや最適化するメリットについて詳しく解説します。
- 物流センター立ち上げ時に気を付けるポイントとは?必要な視点や注意点などについて解説します。
- 「ピッキング作業の際に起こってしまうミス」の原因やミスを減らす改善策について解説します。